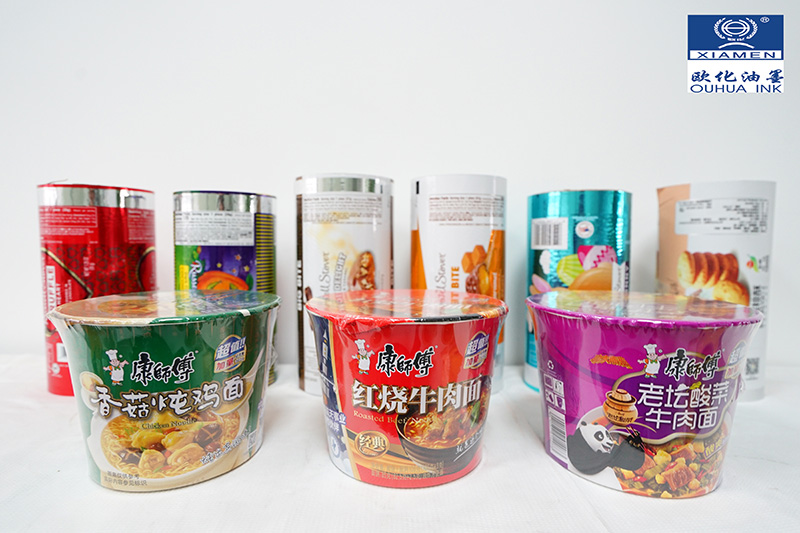
01 No benzene and ketone solvents, little environmental pollution;
02 Universal, suitable for all kinds of composite packaging film printing;
03 Printed products full color, bright color, strong sense of layer;
04 The adaptability of the scraper and the reproducibility of the dot are excellent, and the printing adaptability is good.
05 The single-liquid method can withstand temperature 121℃, if the cooking requirement is higher than 121℃, need to add curing agent;
Good adhesion to the following films:
Polyester (PET) treatment degree above 42 dynes Nylon (NY) treatment degree above 52 dynes
OPP processing degree 38 dyne above K coating (including K cellophane) printing grade
PT cellophane printing grade special polyvinyl alcohol
Suitable for dry compound, solvent-free compound and water glue compound.
PET/ ink /CPP/NY/CPP |
120℃, 30 minutes, contents (water/oil =10/1) |
PET/ ink /NY/AL/CPP |
135℃, 20 minutes, contents (water/oil =10/1) |
PET/ ink /AL/CPP |
135℃, 20 minutes, contents (water/oil =10/1) |
The printing viscosity of color ink and white ink is set at 13 ~ 20 seconds /25℃ 3# Chaen cup.
OHPU#1 |
OHPU#2 |
OHPU#3 |
OHPU#4 |
|
N-propyl acetate |
/ |
70 |
70 |
50 |
Ethyl acetate |
90 |
20 |
/ |
/ |
Butyl acetate |
/ |
/ |
20 |
40 |
Isopropyl alcohol |
10 |
10 |
10 |
10 |
Note: OHPU1# dries fastest, OHPU4# dries slowest.
When the print needs to withstand temperatures above 121 ° C, the curing agent needs to be added to the ink, which can strengthen the temperature resistance of the ink. Please use the OHG#2 curing agent produced by the company, add the amount according to the ratio of ink: curing agent =100:8 ~ 10, the remaining double liquid ink should be sealed and stored, and new ink should be added when used again, it is best not to be used in products that are resistant to cooking.
This product should not be mixed with similar products of other manufacturers. When preparing diluent, please check the quality of the solvent in advance to prevent ink deterioration.
The curing agent will fail when mixed with water. Please seal the remaining curing agent.
Avoid mixing water into the residual ink. Do not use the gelled residual ink. The residual ink should not be used after being stored in unsealed conditions for 48 hours.
New ink and residual ink mixed 2:1, residual ink too much, adhesion decline, may occur sticky back phenomenon;
The ink in the bucket should be shaken before use to ensure quality consistency;
This product should be kept away from fire, sealed, shelf life of one year.